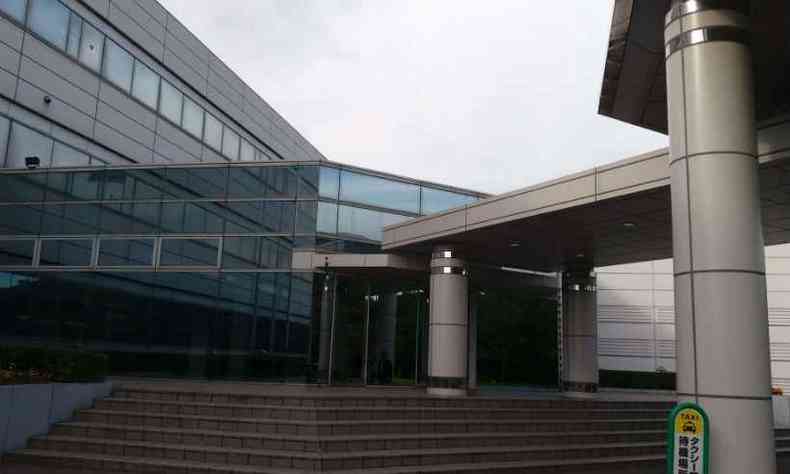
Tóquio, Kimitsu e Futsu – Nem só de aço vive a siderúrgica de Kimitsu, distante cerca de uma hora de Tóquio, na província de Chiba, uma das maiores usinas do mundo, tão grande quanto juntar 200 campos de futebol. Capaz de entregar 9 milhões de toneladas por ano de chapas, barras e tubos, entre outros produtos que serão usados para fazer de carros a navios, sofisticadas pontes e gasodutos, a fábrica é referência também em tecnologia do grupo Nippon Steel & Sumitomo Metal Corporation (NSSMC). O conglomerado disputa degraus da liderança global do setor, atuando no Brasil como acionista de dois grandes empreendimentos, a Usiminas, em Ipatinga, e a Vallourec Soluções Tubulares, em Jeceaba, ambas em Minas Gerais.
A prioridade que eles têm nos gastos do grupo Nippon se traduz num orçamento invejável de US$ 600 milhões por ano para a área de P&D, fortuna que passava, na sexta-feira, do equivalente a R$ 2 bilhões, pelo câmbio de R$ 3,84. É dinheiro suficiente para a construção de 13.300 moradias de baixa renda no Brasil ou a compra de 6,6 mil carros populares. Parte das bem-sucedidas tecnologias produzidas nos centros de pesquisa da siderúrgica japonesa ajudou a erguer o Vale do Aço mineiro, numa troca de saberes que permanece até hoje.
Recuperado e religado neste ano em Ipatinga, o alto-forno 1 da Usiminas, – o equipamento é responsável pela fabricação da matéria-prima essencial do aço, o ferro-gusa –, resultou de um esforço das duas culturas mais de 50 anos atrás. Foi o primeiro alto-forno erguido fora do Japão com tecnologia da Nippon Steel. Durante a construção da siderúrgica mineira, uma equipe de engenheiros contratados para a Usiminas, recém-formados na Escola de Minas de Ouro Preto, foi enviada ao Japão para ser treinada durante dois anos na usina da então Yawata Iron and Steel Company. Eles ficaram conhecidos como os “sete samurais”, em alusão ao clássico filme do cineasta japonês Akira Kurosawa.
Em Kimitsu, enquanto mostra a usina a um grupo de engenheiros da UFMG, que fizeram intercâmbio neste mês no Japão a convite da siderúrgica, e à reportagem do Estado de Minas, Jun Ogura, coordenador de transferência de tecnologia da Nippon, destaca que mais de 1 mil japoneses estiveram no Brasil e voltaram ao país, que se tornaria parceiro do Japão nos últimos 48 anos, o que permitiu troca intensa de tecnologia. “A gente procura desenvolver novos produtos todo dia. O nosso ponto forte é tentar estar à frente (dos concorrentes) em todas as linhas de produção. O objetivo não é ter simplesmente um produto melhor”, afirma.
A Usiminas mantém em Ipatinga um centro de pesquisa e desenvolvimento, considerado, segundo a companhia, o maior no setor siderúrgico da América Latina. Inaugurado em 1971, a unidade ocupa área de 13 mil metros quadrados e detém 17 laboratórios, nos quais simula todo o processo de produção da planta industrial. A empresa detém quase 500 patentes registradas no Brasil e 36 internacionais.
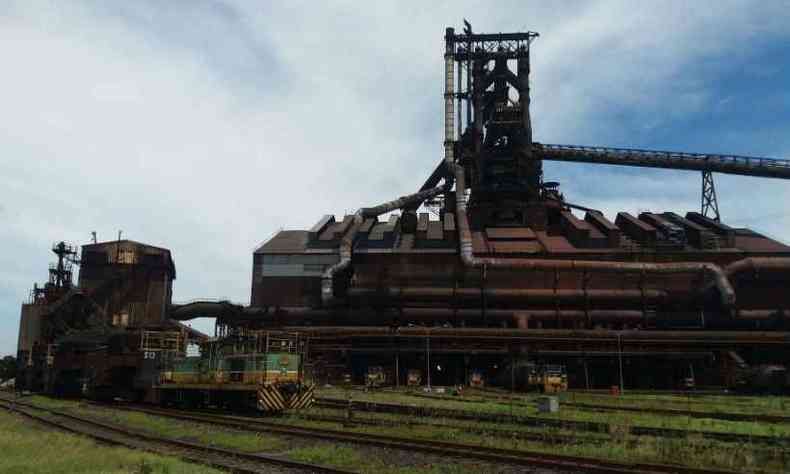
NATUREZA DOMADA No centro de pesquisa e desenvolvimento de Futsu, ainda na província japonesa de Chiba, a imponência do prédio que abriga laboratórios, espécies de pequenas fábricas que reproduzem a produção real da usinas, já demonstra aos visitantes a importância da ciência e da tecnologia para o povo do chamado País do Sol Nascente. Kiyosaburo Azuma, gerente da unidade, conta que 250 engenheiros de equipamentos e máquinas atuam na base, além dos pesquisadores que trabalham nos centros de P&D instalados em cada uma das usinas da empresa no Japão.
“Desenvolvemos produtos com clientes e fazemos projetos nossos aqui, buscando aços mais leves e resistentes para o setor automotivo e a construção naval, evitando o surgimento de trincas”, explica Azuma, conduzindo o grupo pela sala ampla do laboratório de análise de materiais, onde há amostras e ensaios. O visitante curioso vai testar, não sem surpresa, barras de aço mais leves que o alumínio. Os projetos desenvolvidos pelos pesquisadores deram vida, ainda, a aços resistentes ao calor para atender a usinas termelétricas, torres usadas na geração de energia eólica (obtida da força dos ventos) e aços para estruturas marítimas.
Exemplo surpreendente de projeto desafiador feito com aço e desenvolvido com parceria da empresa japonesa, a monumental ponte Akashi-Kaikyo, localizada no estreito de Akashi, entre a cidade de Kobe e a ilha de Awaji, tem vão central de 1.991 metros, o maior no mundo. A obra testou os engenheiros não só pela sofisticação, como também em razão das condições exigentes da natureza no estreito, as fortes correntes, grande profundidade das águas e o risco de furacões e terremotos. O vão é suportado por duas torres de aço de mais de 280 metros de altura.
NO ALTO-FORNO A obtenção do aço percorre longo e cuidadoso processo, que requer em várias etapas altas temperaturas num ambiente que pode se aproximar dos 50 graus. Na usina de Kimitsu, o alto-forno 4, que poderia ser encarado como uma espécie de pulmão da fábrica, surge aos olhos dos visitantes como um gigante produtor de gusa – matéria-prima do aço – alimentado com minério de ferro da Austrália e de Carajás, no Pará. O equipamento se impõe a uma altura de 125 metros, que corresponderiam a um edifício de 41 andares.
No Brasil, o maior alto-forno conhecido está instalado em Vitória (ES), com 100 metros de altura. São necessárias 8 horas para que a carga injetada no equipamento seja totalmente depositada em seu interior, que comporta exatos 5 milhões de litros. Dele saem todo dia 14 mil toneladas de gusa, que mais à frente serão modeladas em aço. O gigante tem seu próprio centro de operação, onde o piso é revestido de carpete e os operadores – são sete ao todo – usam chinelos em tecido e não deixam um único papel ser depositado ao chão. A cada corrida, o gusa é obtido a temperaturas entre 1.500 e 2.000 graus Celsius.
O material segue o caminho das siderúrgicas integradas, chegando aos convertedores, outro tipo de forno onde, à base de pressão altíssima, é injetado oxigênio e são retiradas impurezas, e depois à aciaria, onde o aço é obtido. Na etapa final, o lingotamento contínuo, o aço é solidificado na forma de vários produtos.
BENDITA RECICLAGEM Menina dos olhos da companhia, um incomum processo de reciclagem de plástico foi desenvolvido na usina de Kimitsu, integrado ao processo siderúrgico. A fábrica tem capacidade para processar 13,5 toneladas por hora de plástico recolhido na comunidade e que será misturado a outro insumo da produção de aço, o coque, queimando os gases industriais.
Os resultados da iniciativa são festejados em favor da natureza. Para cada tonelada de aço são geradas duas toneladas de gás carbônico (CO2). Com o uso do novo material, cada tonelada de plástico reciclado reduz três toneladas que seriam emitidas de CO2.
Quem é
A Nippon Steel & Sumitomo Metal Corporation atua em mais de 15 países, mantém 13 usinas no Japão e produziu 46,82 milhões de toneladas de aço bruto em 2017. É mais que toda a produção brasileira, que foi de 34,35 milhões de toneladas no ano passado. O grupo japonês emprega 84 mil funcionários e apurou lucro líquido de 195 bilhões de ienes no exercício fiscal encerrado em 31 de março deste ano, o equivalente a cerca de R$ 6 bilhões.